1 前言
隨著高速加工技術的迅猛發(fā)展,加工過程中使用的切削液用量越來越大,其流量有時高達80~100L/min。但大量切削液的使用造成了非常突出的負面影響:(1)零件的生產成本大幅度提高,在零件加工的總成本中,切削液費用約占16% ,而刀具的費用只占總成本的4%。(2)造成對環(huán)境的嚴重污染,如把未經處理的切削液排入江河湖海,就會污染土地、水源和空氣,嚴重影響動植物的生長,破壞生態(tài)環(huán)境。(3)直接危害車間工人的身體健康,目前生產中廣泛使用的水基切削液含有對人體有害的化學成分。在切削(磨削)過程中,切削液受熱揮發(fā)形成煙霧,在車間常常彌漫著難聞的異味,會引起操作工人肺部和呼吸道的諸多疾病,人手和切削液直接接觸,還會誘發(fā)多種皮膚病,直接影響工人健康。
上述負面影響,已成為機械工業(yè)發(fā)展的一大障礙。這就使人們會提出這樣一個問題:機械加工中能不能不用或少用切削液呢?干切削(Dry Cutting)技術就是在這樣的歷史背景下應運而生,并從90年代中期以來迅速發(fā)展起來的。
干切削技術起源于歐洲,目前在西歐各國也最為盛行。據(jù)統(tǒng)計現(xiàn)在已有8%左右的德國企業(yè)采用了干切削技術。到2003年,德國制造業(yè)將有20%以上采用干切削技術。在干切削研究和應用方面,目前德國處于國際領先地位。
日本已開發(fā)成功不使用切削液的干式加工中心。裝有液氮冷卻的干切削系統(tǒng),從空氣中提取高純度氮氣,常溫下以5~6個大氣壓的壓力將液氮送往切削區(qū),可順利實現(xiàn)干切削。
我國成都工具研究所、山東工業(yè)大學和清華大學等單位對超硬刀具材料及刀具涂層技術進行過系統(tǒng)的研究,陶瓷刀具在我國目前已形成了一定的生產能力,這些都為干切削技術的研究與應用打下了初步的技術基礎。北京機床研究所最近開發(fā)成功了能實現(xiàn)高速干切削的KT系列加工中心。
2 切削液的功能和實現(xiàn)干切削的主要難點
干切削并不是簡單地停止使用切削液就能實現(xiàn)的。必須分析在停用切削液以后,會出現(xiàn)什么問題?應采取什么措施來消除這些不利影響?為此,首先應對切削液在機械加工中的作用和功能有一個全面、深入的認識。
在機械加工中,切削液主要有三大功能:
潤滑功能——當切削液進入切削區(qū)以后,它就會滲入到刀具、工件和切屑之間的接觸面,形成一層潤滑膜。這層潤滑膜可減少切削過程的摩擦,減小切削力,減輕切屑與刀具的粘結現(xiàn)象并抑制積屑瘤的產生,有利于改善加工表面技術質量。
冷卻功能——切削過程所消耗的能量90%以上都轉化為切削熱。切削液能有效地把切削熱從機床的加工區(qū)迅速帶走,從而大大降低機床切削區(qū)的溫升,提高刀具的耐用度和工件的加工精度。
協(xié)助排屑與斷屑——切削液作為高壓大流量的沖洗劑,能把細小的切屑沖離工件或刀具,將切屑迅速從機床中排出,以利于提高零件的加工精度和刀具的使用壽命。帶狀切屑則主要靠刀具的幾何結構來實現(xiàn)斷屑,但高壓切削液對斷屑和排屑也起一定的輔助作用。
進行干切削時,由于缺少了切削液的上述潤滑、冷卻和輔助排屑與斷屑等作用,因而切削熱會急劇增加,機床加工區(qū)溫度明顯上升,刀具耐用度大大降低。要使干切削得以順利進行,達到或超過濕加工時的加工質量、生產率和刀具耐用度,就必須從刀具、機床和工件各方面采取一系列的措施。因此干切削技術是一項龐大的系統(tǒng)工程,其中最大的難點在于如何提高刀具在干切削中的性能,同時也對機床結構、工件材料及工藝過程等提出了新的要求。
3 干切削的刀具技術刀具
能否承受干切削時巨大的熱能,是實現(xiàn)干切削的關鍵。主要措施有:
采用新型的刀具材料
干切削不僅要求刀具材料有很高的紅硬性和熱韌性,而且還必須有良好的耐磨性、耐熱沖擊和抗粘結性。圖1列出了幾種刀具材料的硬度與溫度的關系。由圖可見,陶瓷刀具(Al2O3,Si3N4)、金屬陶瓷(Cermet)等材料的硬度在高溫下也很少降低,即具有很好的紅硬性,因此很適合于一般目的的干切削?墒沁@類材料般較脆,熱韌性不好,不適用于進行斷續(xù)切削。立為氮化硼(CBN)、聚晶金剛石(PCD)、超細晶粒硬質合金等超硬刀具材料則廣泛用于干切削。
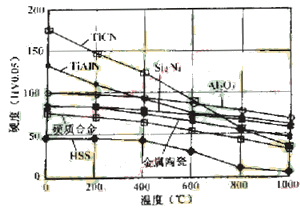
圖1 不同材料硬度與溫度的關系
采用涂層技術
對刀具進行涂層處理,是提高刀具性能的重要途徑。涂層刀具分兩大類:一類是“硬”涂層刀具,如TiN、TiC和Al2O3等徐層刀具。這類刀具表面硬度高,耐磨性好。另一類是“軟”涂層刀具,如:MoS2、WS等涂層刀具,這類涂層刀具也稱為“自潤滑刀具”,它與工件材料的摩擦系數(shù)很低,只有0.01左右,能減小切削力和降低切削溫度。切削實驗表明,無涂層絲錐只能加工加20螺孔;用TiAlN涂層絲錐時可加工1000個螺孔,而MoS2涂層的絲錐則可加工4000個螺孔。高速鋼和硬質合金經過PVD涂層處理后,可以用于干切削。原來只適用于進行鑄鐵干切削的CBN刀具,在經過涂層處理后也可用來加工鋼、鋁合金和其他超硬合。.實際上,涂層有類似于冷卻液的功能.它產生一隔熱層,使熱不會或很少傳入刀具,從而能在較長的時何內保持刀尖的堅硬和鋒利。涂層還有在高速干切削中保待刀具材料不受化學反應的作用。在發(fā)展干切削技術過程中,要特別注意涂層刀具的有效應用。
優(yōu)化刀具參數(shù)和切削用量
刀具的幾何參數(shù)和結構設計必須滿足干切削對斷屑和排屑的要求。斷屑槽在韌性材料加工中對斷屑起著很關鍵的作用。目前在車刀三維曲面斷屑槽方面的設計制造技術已經比較成熟,可針對不同的工件材料和切削用量,很快設計出相應的斷屑槽結構與尺寸,并能大大提高切屑折斷能力和對切屑流動方向的控制能力。
高速加工有切削力小、散熱決、加工過程穩(wěn)定性好等優(yōu)點,高速切削技術與干切削技術的有機結合,將獲得生產效率高、加工質量好和無環(huán)境污染等多重利益。
4 干切削的機床技術
設計干切削機床時要考慮的特殊問題主要有兩個:一個是切削熱的散發(fā);另一個是切屑和灰塵的排出。
干切削時在機床加工區(qū)產生的熱量較大,如不及時從機床的主體結構排出去,就會使機床產生熱變形,影響工件加工精度和機床工作可靠性。對于一些無法排出的熱量,則相關部件應采取隔熱措施。
為了便于排屑。干切削機床應盡可能采用立式主軸和傾斜式床身。工作臺上的傾斜蓋板可用絕熱材料制成.將大量熱切屑直接送入螺旋排屑槽。采用吸氣系統(tǒng)可防止工作臺和其它支承部件上熱切屑的堆積內置的循環(huán)冷氣系統(tǒng)用以提高機床工藝系統(tǒng)的熱穩(wěn)定性。在加工區(qū)的某些關鍵部位設置溫度傳感器,用以監(jiān)控機床溫度場的變化情況,必要時通過數(shù)控系統(tǒng)進行精確的誤差補償。過濾系統(tǒng)可將干切削過程中產生的塵埃顆粒濾掉并被抽風系統(tǒng)及時吸走。產生灰塵的加工區(qū)應和機床的主軸部件及液壓、電氣系統(tǒng)嚴加隔離。此外還可以通過對這些部件施加微壓,以防止灰塵的侵入。
對鋁合金或纖維等增強塑料進行干切削時,必須采用高速加工中心或其它高速數(shù)控機床,其主軸轉速一般高達25000~60000r/min,主電動機功率25~60kW,通常都采用“電主軸”的傳動結構方式;進給速度高達60~100m/min,加速度2~8g(g=9.81m/s2).為普通數(shù)控機床的10倍以上,現(xiàn)已逐步用直線伺服電動機替代滾珠絲杠來實現(xiàn)高速進給運動。
5 干切削的工藝技術
工件材料在很大程度上決定了實施干切削的可能性。干切削的“工件材料/加工方法”的組合如下表所示。由表可見,超硬合金和鋼最難于進行干切削。
難于進行干切削的工件材料和加工方法組合表 |
|
工件材料 |
加工方法 |
|
車削 |
銑削 |
鉸削 |
攻絲 |
鉆孔 |
|
鑄鐵 |
|
|
|
|
|
|
鋼 |
|
× |
× |
× |
|
|
鋁合金 |
|
× |
|
× |
|
|
超硬合金 |
× |
× |
× |
× |
× |
|
復合材料 |
|
|
|
|
|
|
注:×表示難于進行干切削 |
|
鋁合金傳熱系數(shù)高,在加上過程中會吸收大量的切削熱;熱膨漲系數(shù)大,使工件發(fā)生熱變形;硬度和熔點都較低,加工過程中切屑很容易與刀具發(fā)生“膠焊”或粘連,這是鋁合金干切削時遇到的最大難題。解決這難題的最好辦法是采用高速干切削。在高速切削中,95%~98%的切削熱都傳給了切屑,切屑在與刀具前刀面接觸的界面上會被局部熔化.形成一層極薄的液態(tài)薄膜,因而切屑很容易在瞬間被切離工件,大大減小了切削力和產生積屑瘤的可能性。工件可以保持常溫狀態(tài),既提高廠生產效率,又改善了鋁合金工件的加工精度和表面質量。
為了減少高溫下刀具和工件之間材料的擴散和粘結,應特別注意刀具材料與工件之間的合理搭配。例如,金剛石(碳元素C)與鐵元素有很強的化學親合力,故金剛石刀具雖然很硬,但不宜于用來加工鋼鐵工件;鈦合金和某些高溫合金中有鈦元素,因此也不能用含鈦的涂層刀具進行干切削。又如PCBN刀具能夠對淬硬鋼、冷硬鑄鐵和經過表面熱噴涂的硬質工件材料進行干切削,而在加工中、低硬度的工件時,其刀具壽命還不及普通硬質合金的壽命高。
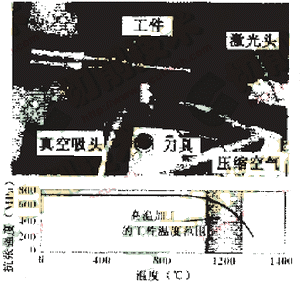
圖2 激光輔助干切削
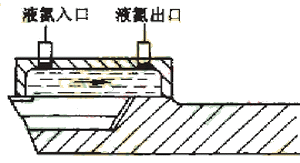
圖3 用液氮冷卻刀具
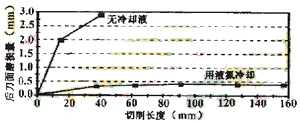
圖4 PCBN刀具在車削RBSN材料后的刀具磨損
硬車是一種“以車代磨”的新工藝,用于某些不適宜進行磨削的回轉休零件的加工,是一種高效的干切削技術。在對氮化硅(Si3N4) 工件進行硬車時.由于該材料有極高的抗拉強度,使任何刀具都很快破損。可采用激光輔助切削,用激光束對工件切削區(qū)進行預熱(見圖2),使工件材料局部軟化 (其抗拉強度由750MPa降至400MPa),則可減小切削阻力30%~70% ,刀具磨損可降低80%左右,干切削過程中的振動也大為減。蟠筇岣吡瞬牧锨谐剩垢汕邢鞯靡皂樌M行。
鈦鋁釩合金(Ti6Al4V)和反應燒結氮化硅(RBSN)是典型的難加工材料,其傳熱系數(shù)很小,干加工中產生大量的熱,使刀具材料發(fā)生化學分解,刀具很決磨損,圖3所示為用液氮冷卻刀具加工這類材料的新方法。
在車刀前刀面上倒裝了個金屬帽狀物,其內腔與刀片的上表面共同組成一個密閉室。帽狀物上有液氮的入口和出口。在干切削過程中,液氮不斷在密閉室中流動,吸收刀片上的切削熱,使刀具不產生過高的溫升.始終保持良好的切削性能,順利實現(xiàn)干切削。圖4是用PCBN刀具加工RBSN工件材料時刀具磨損量的實驗結果。在不使用液氮冷卻刀具時PCBN刀具車削長度僅40mm,后刀面磨損量便高達3mm,切削無法再進行下去。采用上述液氮裝置后,刀具磨損情況大為改善,車削長度160mm后,后刀面僅磨損0.4mm。被加上工件的圓度誤差也從20μm減至3.2μm。液氮是一種很容易獲得的原料價格便宜還可以反復使用。
6 準干切削
純粹的干切削有時很難進行,此時可采用最小量潤滑技術 (Minimal Quantity Lubrication),簡稱MQL。這種方法是將壓縮空氣與少量潤滑液混合氣化后,噴射到加工區(qū),對刀具和工件之間的加工部位進行潤滑。MQL技術可以大大減少“刀具—工件”和“刀具—切屑”之間的摩擦,起到抑制溫升、降低刀具磨損、防止粘連和提高工件加工質量的作用。它所使用的潤滑液很少.而效果卻十分顯著,既提高了工效,又不會對環(huán)境造成污染。例如用(Ti, Al)N+MoS2徐層刀具對鋁合金工件進行純粹的干切削時.刀具鉆16個孔后,切屑就粘結在鉆頭容屑槽中,使刀具完全不能使用。采用MQL技術后.鉆孔數(shù)高達320個.鉆頭也還沒有發(fā)生明顯的磨損或粘連,加上出來的所有孔都滿足要求。
MQL法所使用的潤滑液用量一般為0.03~0.2L/h ,約為濕切削的6萬分之一。清潔和干凈的切屑經過壓縮還可以回收使用,完全不污染環(huán)境。因此MQL法又稱為“準干切削” (Near-Dry Cutting)。
準干切削技術和涂層刀具相結合,能夠取得最好的效果。例如,用高速鋼涂層鉆頭加工X90CrMoV18合金鋼.當用TiAlN涂層高速鋼鉆頭進行純粹干鉆削時,鉆3.5m的叨削長度后鉆失便被損壞;采用(TiAlN+MoS2)復合涂層鉆頭和最小潤滑法,其鉆削長度增加到115m。
7 總結和展望
干切削技術是對傳統(tǒng)生產方式的一個重大創(chuàng)新,是種嶄新的清潔制造技術。世界各國日益嚴厲的環(huán)保法規(guī),有利于加速干切削技術的推廣與應用;各種超硬、耐高溫刀具材料及其涂層技術的發(fā)展,為干切削技術創(chuàng)造了極為有利的條件;最小量潤滑裝置的有效應用和各種中心小孔的孔加工標準刀具的出現(xiàn),使準干切削在鋁合金和各種難加工材料的孔加工中獲得了越來越多的應用。干切削技術從出現(xiàn)到現(xiàn)在只有短短10年的歷史,它是一種新興的綠色制造技術.對實施人類可持續(xù)發(fā)展戰(zhàn)略有重要的意義,是新世紀的前沿制造技術。