圓柱齒輪、錐齒輪和準雙曲面齒輪膠合承載能力計算方法
第1部分:閃溫法
1 范圍
GB/Z 6413本部分根據(jù)布洛克接觸溫度的概念規(guī)定了評價膠合危險的方法和公式。
布洛克的基本概念應(yīng)用于具有移動接觸區(qū)的所有機械零件。閃溫公式對于帶狀或近似帶狀的赫茲接觸區(qū)與足夠高的佩克萊特(peclet)數(shù)為特征的工作條件下是有效的。
2規(guī)范性引用文件
下列文件中的條款通過GB/Z6413本部分的引用而成為本部分的條款,凡是注日期引用文件,其隨后的修改單或修訂版均不適用于本部份,然而,鼓勵根據(jù)本部分達成協(xié)議的各方研究是否可使用這些文件的最新版本。凡是不注日期的引用文件,其最新版本適用于本部分。
GB/T3374—1992 齒輪基本術(shù)語(neq ISO/R1122-1:1983)
GB/T3480—1997 漸開線圓柱齒輪承載能力計算方法(eqv ISO6336-1~6336-3:1996)
GB/T3481—1997 齒輪輪齒磨損和損傷術(shù)語(idt ISO 10825:1995)
GB/T10062.1—2003 錐齒輪承載能力計算方法 第1部分:概述和通用影響系數(shù)(ISO 10300-1:2001,IDT)
3 術(shù)語、定義、代號和單位
3.1 術(shù)語和定義
GB/T3374和GB/T3481中給出的術(shù)語和定義適用于本部分。
3.2代號和單位
本部分所使用的代號見表1。根據(jù)通常做法,長度單位選用米、毫米、和微米。為了整個體系的協(xié)調(diào)性,BM、Cγ和XM的單位適合于米和毫米或毫米和微米的混合使用。
表1 代號和單位
代 號 |
意 義 |
單 位 |
公式(圖)號 |
a |
中心距 |
mm |
式(A.5) |
B |
齒寬,取大輪和小輪中的較小值 |
mm |
式(11) |
Beff |
有效齒寬 |
mm |
式(12) |
bH |
赫茲接觸區(qū)寬度的一半 |
mm |
式(3) |
BM |
熱接觸系數(shù) |
N/(mm1/2·m1/2·s1/2·K) |
式(A.13) |
BM1 |
小輪的熱接觸系數(shù) |
N/(mm1/2·m1/2·s1/2·K) |
式(3) |
BM2 |
大輪的熱接觸系數(shù) |
N/(mm1/2·m1/2·s1/2·K) |
式(3) |
Ca1 |
小輪的齒頂修緣量 |
μm |
式(48) |
Ca2 |
大輪的齒頂修緣量 |
μm |
式(46) |
Ceff |
最佳齒頂修緣量 |
μm |
式(46) |
Ceq1 |
小輪的當(dāng)量齒頂修緣量 |
μm |
式(B.2) |
Ceq2 |
大輪的當(dāng)量齒頂修緣量 |
μm |
式(B.3) |
Cf1 |
小輪的齒根修緣量 |
μm |
式(B.3) |
Cf2 |
大輪的齒根修緣量 |
μm |
式(B.2) |
CM1 |
小輪單位質(zhì)量的比熱 |
J/(kg·K) |
式(9) |
CM2 |
大輪單位質(zhì)量的比熱 |
J/(kg·K) |
式(10) |
C |
嚙合剛度 |
N/(mm·μm) |
式(B.1) |
d1 |
小輪的分度圓直徑 |
mm |
式(34) |
d2 |
大輪的分度圓直徑 |
mm |
式(35) |
da1 |
小輪的齒頂圓直徑 |
mm |
式(34) |
da2 |
大輪的齒頂圓直徑 |
mm |
式(35) |
E1 |
小輪的彈性模具 |
N/mm2 |
式(A1.0) |
E2 |
大輪的彈性模具 |
N/mm2 |
式(A1.0) |
Er |
當(dāng)量彈性模具 |
N/mm2 |
式(A.9) |
Fex |
外加軸向力 |
N |
式(A18) |
Fn |
磨損試驗中的法向載荷 |
N |
圖1 |
Ft |
名義切向力 |
N |
式(11) |
H1 |
輔助參數(shù) |
mm |
式(B.3) |
H2 |
輔助參數(shù) |
mm |
式(B.2) |
ham1 |
小齒輪齒寬中點齒頂高 |
mm |
式(43) |
Ham2 |
大齒輪齒寬中點齒頂高 |
mm |
式(44) |
KA |
使用系數(shù) |
—— |
式(11) |
KBa |
膠合承載能力計算的齒間載荷分配系數(shù) |
—— |
式(11) |
KBβ |
膠合承載能力計算的齒間載荷分布系數(shù) |
—— |
式(11) |
KHa |
接觸強度計算的齒間載荷分配系數(shù) |
—— |
式(15) |
KHβ |
接觸強度計算的齒間載荷分布系數(shù) |
—— |
式(14) |
Kmp |
分支系數(shù) |
—— |
式(11) |
KV |
動載系數(shù) |
—— |
式(11) |
mn |
法向模數(shù) |
mm |
式(B.2) |
n1 |
小齒輪轉(zhuǎn)速 |
r/min |
式(5) |
np |
嚙合分支數(shù) |
—— |
式(16) |
Pe1 |
小輪材料的佩克萊特數(shù) |
—— |
式(9) |
Pe2 |
大輪材料的佩克萊特數(shù) |
—— |
式(10) |
Q |
質(zhì)量等級 |
—— |
式(57) |
Ra1 |
小輪齒面的粗糙度 |
μm |
式(28) |
Ra2 |
大輪齒面的粗糙度 |
μm |
式(28) |
Rm |
中點錐距 |
mm |
式(A.16) |
rm1 |
小輪齒寬中點分度圓半徑 |
mm |
式(43) |
rm2 |
大輪齒寬中點分度圓半徑 |
mm |
式(44) |
SB |
膠合承載能力計算的安全系數(shù) |
—— |
式(100) |
SFZG |
FZG試驗的載荷級 |
—— |
式(99) |
t1 |
小輪的瞬時接觸時間 |
μs |
式(95) |
t2 |
大輪的瞬時接觸時間 |
μs |
式(96) |
tc |
曲線彎曲處的瞬時接觸時間 |
μs |
式(97) |
tmax |
最長瞬時接觸時間 |
μs |
式(95) |
u |
齒數(shù)化 |
—— |
式(A.6) |
uv |
當(dāng)量齒數(shù)比 |
—— |
式(B.6) |
vg |
滑動速度 |
m/s |
圖1 |
vg1 |
小輪的切向速度 |
m/s |
式(3) |
Vg2 |
大輪的切向速度 |
m/s |
式(3) |
Vg∑C |
節(jié)點處的切向速度總和 |
m/s |
式(25) |
vt |
節(jié)圓線速度 |
m/s |
式(26) |
wBn |
法向單位載荷 |
N/mm |
式(3) |
wBt |
端面單位載荷 |
N/mm |
式(5) |
Xbut |
支撐系數(shù) |
—— |
式(54) |
XbutA |
A點的支撐值 |
—— |
式(51) |
XbutB |
B點的支撐值 |
—— |
式(51) |
XG |
幾何系數(shù) |
—— |
式(A.5) |
XJ |
嚙入系數(shù) |
—— |
式(3) |
XL |
潤滑劑系數(shù) |
—— |
式(25) |
XM |
熱彈系數(shù) |
K·N-3/4·s-1/2·m-1/2·mm |
式(5) |
Xmp |
多點嚙合小輪系數(shù) |
—— |
式(22) |
XR |
粗糙度系數(shù) |
—— |
式(25) |
XS |
潤滑方式系數(shù) |
—— |
式(22) |
WX |
組織系數(shù) |
—— |
式(94) |
Xaβ |
角度系數(shù) |
—— |
式(A.6) |
Xг |
載荷分擔(dān)系數(shù) |
—— |
式(3) |
XΘ |
膠合溫度梯度 |
—— |
式(97) |
z1 |
小輪齒數(shù) |
—— |
式(30) |
z2 |
大輪齒數(shù) |
—— |
式(30) |
aa1 |
小輪端面齒頂圓壓力角 |
( °) |
式(31) |
aa2 |
大輪端面齒頂圓壓力角 |
( °) |
式(30) |
at |
端面壓力角 |
( °) |
式(34) |
awn |
法面嚙合角 |
( °) |
式(A.2) |
awt |
端面嚙合角 |
( °) |
式(7) |
ay1 |
小輪任意點壓力角 |
( °) |
式(29) |
β |
螺旋角 |
( °) |
式(18) |
βb |
基圓螺旋角 |
( °) |
式(49) |
βbm |
齒寬中點基圓螺旋角 |
( °) |
式(50) |
βw |
嚙合螺旋角 |
( °) |
式(A.2) |
гA |
嚙合線上A點的參數(shù) |
—— |
式(24) |
ГAA |
嚙合線上AA點的參數(shù) |
—— |
式(68) |
ГAB |
嚙合線上AB點的參數(shù) |
—— |
式(66) |
ГAU |
嚙合線上AU點的參數(shù) |
—— |
式(49) |
ГB |
嚙合線上B點的參數(shù) |
—— |
式(31) |
ГBB |
嚙合線上BB點的參數(shù) |
—— |
式(70) |
ГD |
嚙合線上D點的參數(shù) |
—— |
式(32) |
ГDD |
嚙合線上DD點的參數(shù) |
—— |
式(72) |
ГDE |
嚙合線上DE點的參數(shù) |
—— |
式(67) |
ГE |
嚙合線上E點的參數(shù) |
—— |
式(24) |
ГEE |
嚙合線上EE點的參數(shù) |
—— |
式(74) |
ГEU |
嚙合線上EU點的參數(shù) |
—— |
式(49) |
ГM |
嚙合線上M點的參數(shù) |
—— |
式(86) |
Гy |
嚙合線上任意點的參數(shù) |
—— |
式(7) |
γ1 |
小輪切向速度的方向夾角 |
—— |
式(3) |
γ2 |
大輪切向速度的方向夾角 |
—— |
式(3) |
δ1 |
小輪節(jié)錐角 |
( °) |
式(37) |
δ2 |
大輪節(jié)錐角 |
( °) |
式(39) |
εa |
端面重合度 |
—— |
式(76) |
εβ |
縱向重合度 |
—— |
式(52) |
ηoil |
潤滑油在工作溫度下的絕對(動力)黏度 |
mpa·s |
式(27) |
ΘB |
接觸溫度 |
℃ |
式(1) |
ΘBmax |
接觸最大接觸溫度 |
℃ |
式(2) |
Θfl |
閃溫 |
K |
式(1) |
Θflm |
平均閃溫 |
K |
式(22) |
Θflmax |
最大閃溫 |
K |
式(2) |
ΘflmaxT |
試驗時的最大閃溫溫度 |
K |
式(94) |
ΘM |
本體溫度 |
℃ |
式(22) |
ΘMi |
接觸面的本體溫度 |
℃ |
式(1) |
ΘM1 |
小輪輪齒的本體溫度 |
℃ |
式(20) |
ΘM2 |
大輪輪齒的本體溫度 |
℃ |
式(20) |
ΘMT |
試驗時的本體溫度 |
℃ |
式(94) |
Θoil |
進入嚙合前的油溫 |
℃ |
式(22) |
ΘS |
膠合溫度 |
℃ |
式(94) |
ΘSc |
較長接觸時間的膠合溫度 |
℃ |
式(97) |
λM1 |
小輪的熱傳導(dǎo)系數(shù) |
N/(s·K) |
式(9) |
λM1 |
大輪的熱傳導(dǎo)系數(shù) |
N/(s·K) |
式(10) |
μ |
柱——環(huán)試驗的磨擦因數(shù) |
—— |
圖1 |
μm |
平均磨擦因數(shù) |
—— |
式(3) |
V1 |
小輪材料的泊松比 |
—— |
式(A.10) |
V2 |
大輪材料的泊松比 |
—— |
式(A.10) |
ρM1 |
小輪材料的密度 |
Kg/m3 |
式(9) |
ρM2 |
大輪材料的密度 |
Kg/m3 |
式(10) |
ρrelC |
節(jié)點處的相對曲率半徑 |
mm |
式(25) |
ρy1 |
小輪任意點處的曲率半徑 |
mm |
式(5) |
ρy2 |
大輪任意點處的曲率半徑 |
mm |
式(5) |
ρyrel |
任意點處的相對曲率半徑 |
mm |
式(5) |
∑ |
軸交角 |
( °) |
式(A.15) |
Φ |
齒輪空心套軸的扭轉(zhuǎn)角 |
( °) |
式(17) |
4 膠合和磨損
4.1膠合和磨損的產(chǎn)生
當(dāng)齒輪輪齒完全被潤滑油膜分開時,兩齒面的凹凸不平之間是不接觸的,通常不存在膠合和磨損,此時的磨擦因數(shù)相當(dāng)小。在油膜較厚時,由于突然的熱不穩(wěn)定性[19]引起的類似膠合損傷的這種特殊情況不在此討論。
當(dāng)彈性流體動力油膜較薄時,齒面凹凸之間偶爾會直接接觸,隨著平均油膜厚度的減薄,直接接觸的次數(shù)相應(yīng)增加,則可能會產(chǎn)生磨料磨損、粘著磨損或膠合。由于齒輪輪齒的滾動作用或潤滑油中含有磨粒會引起磨料磨損。粘著磨損是由先局部焊合,隨即分離,從而導(dǎo)致一個或兩個嚙合輪齒上的材料微粒轉(zhuǎn)移而引起的。如果磨粒磨損或粘著磨損是輕微的,且隨著時間的推移而減輕,作為一種正常跑合過程則對輪齒不會造成危害。
與輕微磨損不同,膠合是能導(dǎo)致輪齒擴展性損傷的黏著磨損的嚴重形式。與具有明顯發(fā)展期的點蝕和疲勞折斷不同,瞬時過載會導(dǎo)致膠合失效。
潤滑油中過分進氣或存在污染,諸如懸浮的金屬顆�;蛩矔黾幽z合的危險。高速齒輪膠合后,由于振動而引起更大的動載荷,振動通常會導(dǎo)致進一步的膠合、點蝕、斷齒損傷。
在大多數(shù)情況下,使用具有增強抗膠合添加劑1)的潤滑油能提高齒輪抗膠合承載能力,然而,重要的一點是要意識到使用抗膠合添加劑的一些不足之處:使銅腐蝕、彈性材料的脆化,以及缺乏全球通用性等。
本方法不適用于評價冷膠合,冷膠合通常在低速(節(jié)圓線速度小于4m/s)、質(zhì)量很差的調(diào)質(zhì)重載齒輪上產(chǎn)生。
4.2轉(zhuǎn)換圖
在使用液體潤滑油潤滑的運行條件下,較嚴重的鋼接觸滑動的潤滑狀況可用轉(zhuǎn)換圖描述[20][21][22][23]。圖1所示的轉(zhuǎn)換圖適用于恒定油浴溫度下的接觸運行。
當(dāng)法向力Fn和相對滑動速度vg同時落在A1-S線以下,即圖1的Ⅰ區(qū)時,潤滑狀況的特征可用磨擦因數(shù)大約為0.1、單位磨損率(即:每單位法向力、每單位滑動距離下的體積磨損量)為10-2~10-6mm3(N·m)來表達。
當(dāng)vg不大于S點的值,且載荷增加進入Ⅱ區(qū)時,剛轉(zhuǎn)換進入第二種潤滑狀況。這種輕微磨損潤滑條件的特征可用磨擦因數(shù)大約為0.3~0.4、單位磨損率為1~5 mm3(N·m)來表達。
圖1具有計算接觸溫度實例的逆向形狀轉(zhuǎn)換圖
如果載荷進一步增加,則轉(zhuǎn)換進入第三種潤滑狀況,即進入以A2-S為邊界線的Ⅲ區(qū)。這個區(qū)域的特征可用磨擦因數(shù)等于0.4~0.5來表達,然而,與Ⅰ區(qū)和Ⅱ區(qū)相比磨損率相當(dāng)高,從100~1000 mm3(N·m)。磨損表面呈現(xiàn)膠合形式的嚴重磨損。當(dāng)相對滑動速度超過S點后,如果載荷增加,則直接從Ⅰ區(qū)轉(zhuǎn)換到Ⅲ區(qū)。
有足夠的證據(jù)證明A1-S-A3線的位置取決于潤滑油黏度[24]及赫茲接觸壓力[20][21]。當(dāng)Fn和vg同時落在此線以下時,則認為,齒面由一層較薄的潤滑油膜分隔開,但此膜被粗糙的凹凸部分所穿透。對于這種情況,稱為“邊界彈流動力潤滑”[21]。
在Ⅲ區(qū)中,液體油膜完全推動了作用,這個區(qū)域即為“初始膠合”區(qū)域[25]。有證據(jù)表明以A2-S線為邊界發(fā)生的轉(zhuǎn)換與接觸溫度達到臨界值相關(guān)。這就是布洛克的基本概念。
給出的這個轉(zhuǎn)換圖適用于新的組件(即未氧化鋼的接觸),如齒輪、凸輪及從動件等。這個轉(zhuǎn)換圖符合四球試驗及柱——環(huán)試驗的結(jié)果。
沿A1-S-A3曲線的溫度范圍(從油池溫度開始,依次為整個本體溫度,接觸面本體溫度):在vg=0.001m/s時為28℃到vg=10m/s時的接觸溫度為498℃。這個溫度特性充分表明在恒定的接觸或接觸面本體溫度下,(邊界)彈流動力潤滑未被破壞,例如與化學(xué)吸附性材料的軟化有關(guān)。相反,隨著滑動速度的增加承載能力的明顯降低則認為是由于潤滑油黏度的降低[24] [24] [26] [27] [28] [29]。
與上述情況不同,沿曲線A2-S-A3的計算接觸溫度則趨向于一個恒定的值,即用GCr15鋼時大約為500℃,見圖1。這表明從Ⅱ區(qū)到Ⅲ區(qū)的轉(zhuǎn)換與用鋼的不同有關(guān),從輕微粘著到嚴重粘著,引起了表面磨損機理的變化,也許還包括熱彈不穩(wěn)性機理[30][31]。
因此,結(jié)果表明膠合與接觸溫度的臨界值有關(guān)。對于鋼,用礦物油潤滑時,臨界值大約為500℃,它并不取決于載荷、速度和幾何參數(shù)。
4.3初始膠合時的磨擦
在圖1所示的轉(zhuǎn)換圖中,膠合時,磨擦因數(shù)從0.25跳躍到0.5。相應(yīng)的接觸溫度大約為500℃。這個接觸溫度是測量的接觸面的本體溫度28℃與計算的閃溫470℃的和。
在計算閃溫時所用的磨擦因數(shù)是剛要轉(zhuǎn)換前的磨擦因數(shù),即μ=0.35。如果這種方法不僅要用于柱與環(huán)實驗而且還要用于齒輪傳動(在設(shè)計階段)時,在計算中接觸溫度的臨界值和磨擦因數(shù)值的選取應(yīng)協(xié)商一致。
齒輪承載能力可以預(yù)估:
——當(dāng)使用磨擦因數(shù)μ=0.5時,偏于安全;
——根據(jù)潤滑油的不同,所使用的磨擦因數(shù)為μ=0.25μ~=0.35時,較精確;
——根據(jù)以前的經(jīng)驗,在穩(wěn)定的工作條件下,所用的磨擦因數(shù)較低,那么限定的接觸溫度相應(yīng)地也較低。
根據(jù)經(jīng)驗,對于不加和加少量添加劑和礦物油,油和滾動材料的每一種組合有一個臨界膠合溫度。通常,這個溫度是恒定的,與運行條件、載荷、速度和幾何參數(shù)無關(guān)。
對于加大量添加劑的礦物油和一些種類的復(fù)合油,臨界膠合溫度隨著裝置運行條件變化而變化。因此,此時的臨界溫度必須由模擬齒輪裝置運行條件的實驗分別確定。
5 基本公式
5.1 接觸溫度
在引言中已經(jīng)敘述過,接觸溫度是接觸面的本體溫度ΘMi(見5.4)和閃溫Θfl(見5.2)之和。
ΘB=ΘMi+Θfl……………………………………..(1)
閃溫溫度沿接觸軌跡的變化見圖2。
最大接觸溫度為:
ΘBmax=ΘMi+Θflmax……………………………………..(2)
式中:
Θflmax——Θfl的最大值,它不是位于嚙入軌跡上就是位于嚙出軌跡上。
膠合的可能性可通過計算最大接觸溫度和其臨界值的比較進行預(yù)測。接觸溫度的臨界值可通過齒輪膠合實驗確定,或通過使用現(xiàn)場的調(diào)查研究確定。
a 在嚙合線上的位置
圖2沿接觸軌跡的接觸溫度
對于膠合危險性的可靠評價,重要的是在分析中,要使用齒輪本體溫度的精確值。
5.2閃溫公式
對于(近似)帶狀接觸區(qū)和不同方向的切向速度(如準雙曲面齒輪),布洛克閃溫公式[12][14][16][32]最常用的表達式見附錄A,即:

……………….(3)
對于具有帶狀接觸區(qū)和切向速度平行的圓柱齒輪和錐齒輪,常用的表達式見附錄A,即:

…………………………….....(4)
或用等效表達式:

………(5)
式中:
μm——平均磨擦因數(shù)(見第6章);
XM——熱彈系數(shù)(見附錄A),對于常用鋼:XM=50K·N-3/4·S1/2·m-1/2·mm;
XJ——嚙入系數(shù)(見第8章);
Xг——載荷分擔(dān)系數(shù)(見第9章);
wBt——端面單位載荷(見5.3),單位為牛每毫米(N/mm);
n1——小輪轉(zhuǎn)速,單位為轉(zhuǎn)每分(rimin);
ρyrel——局部相對曲率半徑,單位為毫米(mm);

……………………………….(6)
ρy1——小輪齒廓局部曲率半徑,單位為毫米(mm);
對圓柱齒輪:
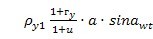
…………………(7)
ρy2——小輪齒廓局部曲率半徑,單位為毫米(mm);
對圓柱齒輪:
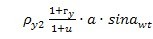
…………………(8)
對于錐齒輪,ρy1和ρy2見式(37)和式(38)。
對于Θn更適用的表達形式,見附錄A。
兩個佩克萊特數(shù)必須足夠高,以使它能滿足幾乎所有可能發(fā)生膠合的情況。當(dāng)佩克萊特數(shù)較低時,熱量從接觸帶區(qū)流向整個輪齒,引起不同的溫度分布,此時式(3)和式(6)無效。

……………………..(9)
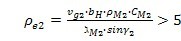
……………………..(10)
式中:
ρM1——小輪材料的密度,單位為千克每立方米(kg/m3);
ρM2——大輪材料的密度,單位為千克每立方米(kg/m3);
CM1——小輪單位質(zhì)量的比熱,單位為焦耳每千克開爾文[J/(kg·K)];
CM2——大輪單位質(zhì)量的比熱,單位為焦耳每千克開爾文[J/(kg·K)];
λM1——小輪的熱導(dǎo)率,單位為千每秒開爾文[N/(S·K)];
λM2——大輪的熱導(dǎo)率,單位為千每秒開爾文[N/(S·K)];
對于圓柱齒輪和錐齒輪sinγ1= sinγ2=1.
5.3 端面單位載荷
圓柱齒輪端面單位載荷:

……………………………(11)
錐齒輪端面單位載荷:

……………………………(12)
式中:
Ft——節(jié)圓上的名義切向力,單位為牛(N);
b——齒寬,單位為毫米(mm);
beff=0.85b……………………………………(13)
KA——使用系數(shù)(對于圓柱齒輪,見GB/T3480,對于錐齒輪,見GB/T10062.1);
KV——動載系數(shù)(對于圓柱齒輪,見GB/T3480,對于錐齒輪,見GB/T10062.1);
KBβ——膠合承載能力計算的齒向載荷分布系數(shù);
KBβ= KHβ………………………………………..(14)
圓柱齒輪和錐齒輪的KHβ分別見GB/T3480和GB/T10062.1);
KBa——膠合承載能力計算的齒間載荷分配系數(shù);
KBa= KHa…………………………………………..(15)
圓柱齒輪和錐齒輪的KHa分別見GB/T3480和GB/T10062.1);
Kmp——分支系數(shù)。
分支系數(shù)Kmp是考慮多分支傳動時,每個分支上載荷分配不均勻的系數(shù)。如果沒有可靠的分析數(shù)據(jù)可用時,可用下列方法確定:
——對于具有np(np3)個行星齒輪的行星齒輪傳動:

……………………………………(16)
——對于在滿載下,齒輪空心軸扭轉(zhuǎn)角為Φ(°)的雙聯(lián)齒輪:
Kmp =1+(0.2/Φ) …………………………………………(17)
——對于外加軸向力為Fex的雙斜齒輪:
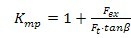
………………………………………………(18)
——對于其他情況:
Kmp =1……………………………………………(19)
5.4 本體溫度的分布
齒輪傳動最主要的磨擦損失是輪齒嚙合區(qū)的磨擦損失。其損失形式主要由于輪齒的磨擦而產(chǎn)生熱量。由于多余的供油側(cè)面排放消耗的機械“泵”能,有時不能忽略。由軸承(滾動軸承或滑動軸承)產(chǎn)生的損失是另一種不可避免的磨擦損失。對于高速齒輪傳動,滑動軸承產(chǎn)生的熱量可能比齒輪嚙合產(chǎn)生的熱量大得多。另一些熱源是攪油和油封的磨擦。所有以上熱源有下列共同特點:
——對于每種熱源,流體的磨擦取決于各自動轉(zhuǎn)條件下的潤滑油黏度;
——所有熱源的熱量是相互聯(lián)系的,通過傳動元件到散熱裝置,如周圍的空氣或冷卻系統(tǒng)。
熱量的相互聯(lián)系可用下列計算方法:
——離散組元的有限元法;
——擴散圖法;
——熱網(wǎng)絡(luò)類比法[18]。
接觸面的本體溫度ΘMi可能適當(dāng)?shù)厝蓚€相接觸輪齒的整體本體溫度ΘM1和ΘM2的平均值。
下式為較精確的近似公式(在佩克萊特數(shù)較高時):
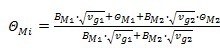
……………………………(20)
當(dāng) 的比值在一個相當(dāng)廣的范圍內(nèi)時,可用簡單的數(shù)學(xué)平均式來近似計算:

………………………………………(21)
當(dāng)閃溫長期超過150℃時,可能對齒面疲勞有不利的影響。
5.5 本體溫度的粗略近似
為了粗略地研究本體溫度,可用油溫(要考慮噴油潤滑對熱傳遞帶來的一些阻礙因素)加上決定閃溫溫度的那一部分取最大值之和來估算。
ΘM=Θoil+0.47Xs·Xmp·Θflm…………………………..(22)
式中:
對于噴油潤滑:Xs =1.2;
對于油浴潤滑:Xs =1;
對于具有附加噴油潤滑冷卻的嚙合:Xs =1.0;
對于為提供足夠的冷卻而將齒輪浸沒在油中時:Xs =0.2;
對于一個小輪與np個大輪嚙合:

………………………………………(23)
Θflm——沿接觸軌跡的平均閃溫,單位為攝氏度(℃)
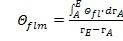
………………………………..(24)
然而,為了可靠地評價膠合的危險性,重要的是在分析中,要用齒輪本體溫度的精確值來替代粗略的近似值。
6 磨擦因數(shù)
在一個嚙合周期內(nèi),影響齒輪輪齒間磨擦的一些因素是變化的。兩個嚙合齒面間存在相對運動,且在一個齒面是均勻的加速,而在別一個齒面上是均勻的減速。僅在節(jié)點位置是純滾動。在任何其他位置都存在滾動和滑動。作用在兩嚙合齒面上的載荷也隨著嚙合位置的變化而變化。這些因素引起油膜厚度、潤滑狀態(tài)和磨擦因數(shù)的連續(xù)變化。即使在相同的嚙合位置,對于不同的輪和不同時間,磨擦因數(shù)也可能是變化的。
為消除各種影響,認為局部磨擦因數(shù)適用于相關(guān)局部點處磨擦因數(shù)的示值。通過計算或測量來幾何確定局部磨擦因數(shù)的變化是很困難的。因此,用代表性的磨擦因數(shù)的平均值來代替局部磨擦因數(shù)的值。
通常所使用的是磨擦因數(shù)的平均值(沿接觸軌跡),即使這個值是變化的。在實驗報告中,常常忽略了一些重要的影響因素,例如確定入口黏度的本體溫度和潤滑狀況。
平均磨擦因數(shù)2)(2)平均磨擦因數(shù)定義為沿接觸軌跡局部磨擦因數(shù)的平均值。盡管節(jié)點處的實際局部磨擦因數(shù)與定義在整個接觸軌跡上的平均磨擦因數(shù)不同,但平均磨擦因數(shù)可按節(jié)點來表達。)μm取決于端面嚙合線的幾何參數(shù)、切向速度、法向載荷、入品黏度(相同于輪齒在本體溫度處的黏度)、壓黏系數(shù)、當(dāng)量彈性模量、表面粗糙度、法向相對曲率半徑。其他的一些影響因素(如公式中的和使用現(xiàn)場的)也必須要考慮,當(dāng)然,要取決于進一步的研究。通過量綱的分析[33],有些很小的影響量可能被略去,影響量的數(shù)目可能會減少。
可用各種方法來測量和估算磨擦因數(shù),應(yīng)根據(jù)磨擦因數(shù)來選擇極限接觸溫度。
6.1 平均磨擦因數(shù),A法
用齒輪實驗或柱——環(huán)實驗方法測出開始膠合時的磨擦因數(shù)。此法的極限接觸溫度相對較高。
6.2 平均磨擦因數(shù),B法
根據(jù)經(jīng)驗,在有規(guī)則的工作條件下使用較小的磨擦因數(shù),最后計算磨擦因數(shù)可用一些合適的公式進行,即這些公式包含了相當(dāng)于齒輪本體溫度的絕對(動力)黏度ηL。此法的極限接觸溫度相對較低,見第10章。
6.3 平均磨擦因數(shù),C法
如果計算開始時,還不知道本體溫度,通常工作條件下的平均磨擦因數(shù)可用下式計算:

……………………………(25)
式中:
wBt——切向單位載荷,見式(11)或式(12),單位為牛每毫米(N/mm);
vg∑C——節(jié)點的切向速度之和,單位為米每秒(m/s);
vg∑C =2·vt·sinawt………………………………(26)
vt——節(jié)圓線速度,單位為米每秒(m/s),如果vt>50m/s時,在式(26)中取vt=50m/s;
ρrelC——端面相對曲率半徑(當(dāng)гy=0時,按式(6)計算),單位為毫米(mm);
XL——潤滑劑系數(shù):
對于礦物油:XL=1.0(ηoil)-0.05
對于水溶性聚(乙)二醇:XL=0.6(ηoil)-0.05
對于非水溶性聚(乙)二醇:XL=0.7(ηoil)-0.05
對于聚a稀族烴:XL=0.8(ηoil)-0.05 ……………………(27)
對于磷酸酯:XL=1.3(ηoil)-0.05
對于牽引液:XL=1.5(ηoil)-0.05
ηoil——在油溫Θoil下的動力黏度,單位為毫帕秒(mPa·s);
XR——粗糙度系數(shù)
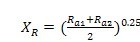
………………………………………..(28)
式中:
Ra1——跑合前的小輪齒面粗糙度Ra,單位為微米(μm)(適當(dāng)跑合后Ra1可降低到初始值的大約60%);
Ra2——跑合前的小輪齒面粗糙度Ra,單位為微米(μm)(適當(dāng)跑合后Ra2可降低到初始值的大約60%);
7 嚙合線上的參數(shù)
嚙合線上的點用無量綱線性參數(shù)гy來表示,在嚙合線與小輪基圓的切點處гy為-1,在節(jié)點處гy為0[33],見圖3。
a 基節(jié)
圖3 嚙合線上的參數(shù)
在接觸軌跡上的任意點處:
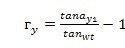
……………………………………………………(29)
在接觸軌跡的下界點處:
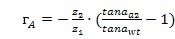
……………………………………………………(30)
在單對齒嚙合區(qū)下界點處:
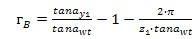
……………………………………………………(31)
在單對齒嚙合區(qū)上界點處:
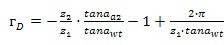
……………………………………………………(32)
在接觸軌跡的上界點處:
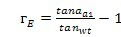
……………………………………………(33)
上述式中,齒頂壓力角定義為:
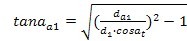
……………………………..(34)
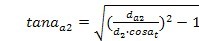
……………………………..(35)
錐齒輪的參數(shù)既可以用當(dāng)量幾何參數(shù)來計算(見GB/T 10062.1附錄A),也可以用下述公式計算(也適用于軸交角∑=δ1+δ2不等于90°時的情況)。
在嚙合線上的任意點處:
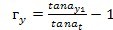
……………………………………………………(36)
ρy1=Rm·tanδ1·sinat·(1+гy) …………………………………………(37)
ρy2=Rm·tanδ1·sinat·(u+гy) …………………………………………(38)
在嚙合線上的特征點處:

……………………………………………………(39)

……………………………………………………(40)

……………………………………………………(41)
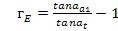
…………………………………………(42)
上述式中,壓力角被定義為:

……………………………..(43)

……………………………..(44)
式中:
δ1——小輪的節(jié)錐角,單位為度(°);
δ2——大輪的節(jié)錐角,單位為度(°);
Rm——中點(齒寬中心)錐距,單位為毫米(mm);
ham1——小輪齒寬中點齒頂高,單位為毫米(mm);
ham2——大輪齒寬中點齒頂高,單位為毫米(mm);
rm1——小輪齒寬中點節(jié)圓半徑,單位為毫米(mm);
rm2——大輪齒寬中點節(jié)圓半徑,單位為毫米(mm)。
8 嚙入系數(shù)
嚙入系數(shù)是根據(jù)經(jīng)驗考慮,由于嚙合開始時齒面上還未形成油膜而使膠合的危險性增加的系數(shù)。對于較大的齒輪其影響相對較大。
嚙入系數(shù)為:
——對于小輪驅(qū)動大輪(減速)
當(dāng)гy≥0時
XJ=1……………………………………(45)
當(dāng)гy<0時

…………………….(46)
當(dāng)гy≤0時
XJ=1……………………………………(47)
當(dāng)гy>0時

…………………….(48)
式中:
Ceff——最佳齒頂修緣量(見附錄B),單位為微米(μm);
Ca1——小輪的齒頂修緣量,單位為微米(μm);
Ca2——大輪的齒頂修緣量,單位為微米(μm);
當(dāng)гy——嚙合線上任意點的參數(shù)(見第7章);
當(dāng)гA—嚙合線上A點的參數(shù)(見第7章);
當(dāng)гB—嚙合線上B點的參數(shù)(見第7章)。
9 載荷分擔(dān)系數(shù)
載荷分擔(dān)系數(shù)Xг是考慮后續(xù)嚙合的輪齒上的載荷分擔(dān)的系數(shù)。根據(jù)常規(guī),載荷分擔(dān)系數(shù)表示為嚙合線上的線性參數(shù)гy的函數(shù)。當(dāng)前面的輪齒結(jié)束嚙合時,在端面雙齒嚙合區(qū)的嚙入軌跡上,載荷分擔(dān)系數(shù)增加,當(dāng)后面的輪齒進入嚙合時,在端面雙齒嚙合區(qū)的嚙出軌跡上,載荷分擔(dān)系數(shù)減少。
由于前面嚙合的輪齒的誤差,可能引起理論載荷分擔(dān)系數(shù)的瞬時增加或減少,這與由稍晚一點進入嚙合的后續(xù)輪齒的誤差引起的載荷分擔(dān)系數(shù)的瞬時增加或減少無關(guān)。
對于圓柱齒輪,Xг的值不超過1.00,它指的是所有端面單對齒嚙合區(qū)。由于動載荷不規(guī)則變化的位置可能引起端面單對齒嚙合區(qū)的擴大。
載荷分擔(dān)系數(shù)Xг取決于齒輪傳動類型和齒廓修形。在有斜齒(偏向齒體內(nèi)齒廓修形)支撐的情況下,載荷分擔(dān)系數(shù)與支撐系數(shù)Xbut一起考慮。
齒廓修形(齒項修緣)公式見附錄B。
9.1 支撐系數(shù)
對于斜齒輪,由于接觸線的傾斜,在嚙合線上的兩端A點和E點附近可能有一個支撐的影響。這個影響適用于齒頂修緣量小于最佳值(Ca<Ceff)時的圓柱齒輪和錐齒輪。
支撐系數(shù)用Xbut表示,可簡化為A-AU、AU-EU、EU-E范圍內(nèi)的線性函數(shù),見圖4。
圖4 支撐函數(shù)
Xbut可用下述式子表達:
對圓柱齒輪
гAU-гA=гE-гEU=0.2sinβb…………………………………..(49)
對錐齒輪
гAU-гA=гE-гEU=0.2sinβb…………………………………..(50)
當(dāng)εβ≥1時
XbutA=XbutE=1.3………………………………………………………….(51)
當(dāng)εβ<1時
XbutA=XbutE=1+1.3εβ…………………………………………………..(52)
XbutAU=XbutEU=1………………………..…………………………………..(53)
對于гA≤гy<гAU時

…………………………………(54)
對于гAU≤гy≤гEU時
Xbut=1………………………..…………………………………..(55)
對于гEU<гy≤гE時

…………………………………(56)
9.2 齒廓未修形的直齒輪
通常認為齒廓未修形的直齒輪的載荷分擔(dān)系數(shù)值是個不連續(xù)的矩形,見圖5。然而,由于存在制造誤差,在每個雙嚙區(qū)內(nèi),對于凸出的齒廓,載荷分擔(dān)系數(shù)將增加,對于其他齒輪,載荷分擔(dān)系數(shù)將減少[34]。不同精度等級齒輪的載荷分擔(dān)系數(shù)是一個包絡(luò)線族,見圖6。
圖5 齒廓未修形的直齒圓柱齒輪的載荷分擔(dān)系數(shù)(精度等級Q為7級或7級以上)
圖6 齒廓未修形的直齒圓柱齒輪的載荷分擔(dān)系數(shù)(精度等級Q為8級或8級以上)
對于гA≤гy<гB
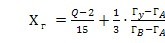
………………………………………(57)
對于гB<гy≤гD
Xг=1………………………..…………………………………..(58)
對于гD≤гy≤гE
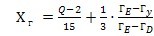
………………………………………(59)
當(dāng)精度等級Q為7級或7級以上時
Q=7…………………………………………(60)
當(dāng)精度等級Q為8級或8級以下時,取Q=精度等級。
9.3 齒廓修形的直齒輪
見圖7和圖8
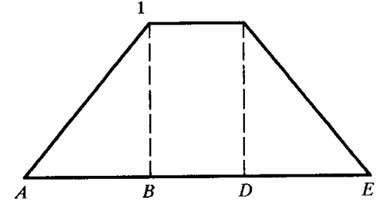
圖7 具有最佳齒廓修形的直齒圓柱齒輪的載荷分擔(dān)系數(shù)
圖8 在A點附近具有偏向體外的齒廓修形,而在E點附近具有偏向體內(nèi)的齒廓修形的直齒圓柱齒輪的載荷分擔(dān)系數(shù)
對于гA≤гy≤гAB

………………………………………(61)
對于гAB≤гy≤гB

………………………………………(62)
對于гB≤гy≤гD

=1…………………………………………..(63)
對于гD≤гy≤гDE

………………………………………(64)
對于гDE≤гy≤гD

………………………………………(65)
гAB=0.5·(гA+гB)……………………………………………….(66)
гDE=0.5·(гD+гE)………………………………………………..(67)
對于Ca2>Ceff
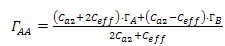
……………………………….(68)
對于Ca2≤Ceff
гAA=гA……………………………………………………………………..(69)
對于Ca1>Ceff

……………………………….(70)
對于Ca1≤Ceff
гBB=гB……………………………………………………………………..(71)
對于Ca2>Ceff
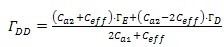
……………………………….(72)
對于Ca2≤Ceff
гDD=гD……………………………………………………………………..(73)
對于Ca1>Ceff

……………………………….(74)
對于Ca1<Ceff
гEE=гE……………………………………………………………………..(75)
9.4 齒廓未修形的窄斜齒輪
對于總重合度較小(εy<2)的斜齒輪仍然有單齒嚙合區(qū).因此,考慮到端面的幾何參數(shù)以及支撐的影響,這種斜齒輪可以與直齒輪類似處理.見圖9.
未修形的窄斜齒輪的載荷分擔(dān)系數(shù)由9.2中的XГ乘以支撐系數(shù)Xbut獲得.
圖9齒廓未修形并考慮支撐影響的窄斜齒輪的載荷分擔(dān)系數(shù)
9.5 齒廓修形的窄斜齒輪
總重合度較小(εy<2)的斜齒輪仍然有單齒嚙合區(qū).因此,考慮到端面的幾何參數(shù),這種斜齒輪可以與直齒輪類似處理.見圖10和見圖11.
這種齒輪的載荷分擔(dān)系數(shù)由9.2中的XГ乘支撐系數(shù)Xbut獲得.
圖10 具有最佳或偏向體外的齒廓修形的窄斜圓柱齒輪的載荷分擔(dān)系數(shù)
圖11 具有偏向體內(nèi)的齒廓修形的窄斜齒輪的載荷分擔(dān)系數(shù)
9.6 齒廓未修形的寬斜齒輪
對于寬斜齒輪(εy<2),在傾斜接觸線的末端,局部嚙合剛度較高, , , , ,此時,假定支撐的影響[35]作用在沿斜齒的A點和E點附近的一個恒定長度上,這個長度相對于端面的長度為0.2sinβb,見圖12、圖4和9.1。
圖12 齒廓未修形的圓柱寬斜齒輪的載荷分擔(dān)系數(shù)
此時,載荷分擔(dān)系數(shù)由表示平均載荷的值1/εa乘以支撐系數(shù)Xbut獲得:
X
r=

……………………(76)
9.7 齒廓修形的寬斜齒輪
假定在接觸軌跡兩端的A-AB段和DE-E段的齒頂修緣長度相等,并導(dǎo)致未加載齒輪的商面重合度為ε
a=1,見圖13。具有偏向體內(nèi)或偏向體外齒廓修形的圓柱寬斜齒輪(ε
y>2)的載荷分擔(dān)系數(shù),在具有支撐影響的未修形齒廓和最佳齒廓修形的載荷分擔(dān)系數(shù)之間分別用內(nèi)插法或外插法確定,見圖14。
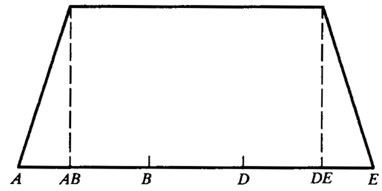
圖13 具有最佳齒廓修形的圓柱寬斜齒輪的載荷分擔(dān)系數(shù)
圖14 在A點附近具有偏向體外、在E點附近具有偏向體內(nèi)的
齒廓修形的圓柱寬斜齒輪的載荷分擔(dān)系數(shù)
用以下的各點來區(qū)分這些不同的范圍:
ГAB=0.5(ГA+ГB)………………………………….(77)
ГDE=0.5(ГD+ГE)………………………………….(78)
對于Ca2≥Ceff

………………….(79)
對于Ca1≥Ceff

………………….(80)
對于Ca1<Ceff,ГAA≤Гy≤ГAB或?qū)τ贑a2≥Ceff,ГA≤Гy≤ГAB

……………..(81)
對于Ca2<Ceff,ГAA≤Гy≤ГAB
XΓ=0…………………………………(82)
對于Ca2≥Ceff,ГAB≤Гy≤ГDE

………………….(83)
對于Ca1<Ceff,ГDE≤Гy≤ГE或?qū)τ贑a1≥Ceff,ГDE≤Гy≤ГEE

………………….(84)
對于Ca2≥Ceff, ГDE≤Гy≤ГEE
XГ=0………….………………………………….(85)
9.8 窄錐齒輪
具有齒廓修形(Ca2 <Ceff)的窄錐齒輪(εy<2),載荷分擔(dān)系數(shù)XГ在按9.4計算的XГ(Ca=0)和按9.9計算的XГ(Ca= Ceff)之間用線性內(nèi)插法確定。記住Xbut.
具有齒廓修形(Ca2≥Ceff) 的窄錐齒輪(εy<2),載荷分擔(dān)系數(shù)XГ在按9.9計算。
9.9 寬錐齒輪
具有最佳齒廓修形(Ca1=Ceff ,Ca2=Ceff) 的寬錐齒輪,假定載荷分擔(dān)系數(shù)為拋物線形[35],見圖15。
中點M的定義為:

…………………….………………….(86)
圖15具有最佳齒廓修形錐齒輪的載荷分擔(dān)系數(shù)
最佳齒廓修形(C
a1=C
eff ,C
a2=C
eff)的載荷分擔(dān)系數(shù):
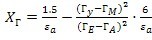
………………….(87)
如果齒廓修形量Ca1與Ca2不同,那么在M點曲線不連續(xù),AM段和ME段應(yīng)分別計算,見圖16。
圖16 在A點附近具有偏向體內(nèi)的齒廓修形、在E點附近具有偏向體外的
齒廓修形錐齒輪的載荷分擔(dān)系數(shù)
對于偏向體內(nèi)的齒廓修形,載荷分擔(dān)系數(shù)在具有支撐影響(見9.6)的未修形齒廓的載荷分擔(dān)系數(shù)和最佳修形齒廓的拋物線形載荷分擔(dān)系數(shù)之間用內(nèi)插法確定。
對于偏向體外的齒廓修形,拋物線形有一個新的端點AA或EE。
對于偏向體內(nèi)的齒廓修形,XГ在具有最佳齒廓修形的XГ(公式87)和齒廓未修形時的XГ(公式76)之間用線性內(nèi)插法確定。插值確定應(yīng)分段進行,即受Ca2影響的AM段和受Ca1影響的ME段。
對于偏向體內(nèi)的齒廓修形,則有新的端點AA和EE。

…………………….………………….(88)

…………………….………………….(89)
對于ГA≤Гy≤ГAA
XГ=0………….………………………………….(90)
對于ГAA<ГA≤ГM

…………………….………(91)
對于ГM<ГA≤ГEE

…………………….………(92)
對于ГEE<Гy≤ГE
XГ=0………….………………………………….(93)
10膠合溫度和安全性
10.1 膠合溫度
膠合溫度是根據(jù)所選擇的潤滑油和齒輪材料的組合可能發(fā)生膠合時的接觸溫度。認為一對齒輪的材料-潤滑油-材料系統(tǒng)的膠合溫度有一個特定的值,這個值由相同材料-潤滑油-材料系統(tǒng)的齒輪試驗來確定[36]。
當(dāng)使用較低添加劑的礦物油時,認為在相當(dāng)廣的范圍內(nèi)膠合溫度與工作條件無關(guān)。
當(dāng)使用具有抗膠合或減磨添加劑的礦物油或合成油時,對于不同的材料和工作條件下,膠合溫度可能是非恒定值這一特性的確定仍需要一步研究。尤其應(yīng)注意的是試驗條件和實際工作條件或設(shè)計條件之間的修正,轉(zhuǎn)換圖中(見圖1)所顯示的特性可能對這種修正的影響很大。
10.2 組織系數(shù)
引入經(jīng)驗性的組織系數(shù)后,具有較低添加劑礦物潤滑油,由齒輪試驗確定的膠合溫度,可擴展到不同的齒輪鋼、熱處理或表面處理。
ΘS=ΘMT + XWΘflmaxT………………………………….(94)
式中:
ΘMT——試驗齒輪的閃溫,單位為攝氏度(℃);
ΘflmaxT——試驗齒輪的最大閃溫,單位為開爾文(K);
XW——組織系數(shù)(見表2)。
然而,對于通常的工作條件和使用熱彈系數(shù)的平均值時,組織系數(shù)的這個近似值受所用磨擦因數(shù)的方法的限制。如果所使用的方法是考慮磨擦因數(shù)和熱彈系數(shù)的真實值時,則不必再使用組織系數(shù)。
表2組織系數(shù)
材 料 |
XW |
調(diào)質(zhì)鋼 |
1.00 |
磷化鋼 |
1.25 |
鍍銅鋼 |
1.50 |
液體或氣體氮化鋼 |
1.50 |
滲碳淬火鋼,奧氏體含量:
——低于平均值
——平均值(10%~20%)
——高于平均值 |
1.15
1.00
0.85 |
奧氏體鋼(不銹鋼) |
0.45 |
10.3 瞬時接觸時間
試驗[37]表明:用抗膠合油潤滑時,齒輪的膠合溫度受瞬時接觸時間的影響。瞬時接觸時間是指齒面上的一點暴露在相嚙齒的赫茲接觸帶內(nèi)的時間。
一對齒面確定的瞬時接觸時間tmax為t1和t2中的最大值。
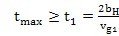
…………….……………….………(95)
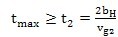
…………….……………….………(96)
膠合溫度ΘS和接觸溫度之間關(guān)系可近似地用圖17所示的由兩條直線組成的曲線表達。
對于tmax<tC
ΘS=ΘSC+XΘXW(tC -tmax)……………………………………………(97)
tmax≥tC
ΘS=ΘSC……………………………………………(98)
式中:
ΘSC——較長接觸時間的膠合溫度,單位為報氏度(℃);
XΘ——膠合溫度梯度,單位為開爾文每微秒(K/μs);
XW——組織系數(shù);
tc——曲線變曲處的瞬時接觸時間,單位為微秒(μs);
tmax——嚙合齒的瞬時接觸時間,單位為微秒(μs)。
對于不同的潤滑油XΘ和tc可用下列值:
——不加抗膠合添加劑:XΘ=0 K/μs,tc=18μs;
——加抗膠合添加劑:XΘ=18 K/μs,tc=18μs。
圖17 對于加抗膠合添加劑潤滑油瞬時接觸時間對膠合溫度的影響
10.4 齒輪試驗的膠合溫度
膠合溫度可由齒輪試驗確定,如Ryder[38],F(xiàn)ZG-Ryder[39],F(xiàn)ZGL-42[40],F(xiàn)ZGA/8.3/90[41]等方法。
試驗結(jié)果的表達應(yīng)包括膠合溫度和試驗條件。如果試驗結(jié)果用其他方式表達,則應(yīng)給出關(guān)系式,如:
ΘS=80+(0.85+1.4XW)·XL·(SFZG)2…………………………………(99)
式中:
XW——組合系數(shù)(見表2);
XL——潤滑油系數(shù)(見式27);
SFZG——FZG A/8.3/90試驗的載荷級。這里指的是發(fā)生膠合時載荷級。
然而,油有參數(shù)變化容易引起SFZG更大的變化,假定在換油間隔期間油稍微有點變質(zhì),載荷級的變化通常為±1。因此,計算時間可用比規(guī)定載荷級較小的載荷級。
10.5 安全范圍
與疲勞損傷的時間較長相比,一次簡單的瞬時過載就會引起嚴重的膠合使齒輪在較矩的時間失效。因此在選擇合適的安全范圍時,應(yīng)謹慎考慮,尤其要注意運行時節(jié)線速度較高的齒輪。
在較知瞬時接觸時間tmax情況下,安全條件是基于膠合溫度的增加(ΘS>ΘSC)(見10.3),而瞬時接觸溫度tmax不應(yīng)該增加,除非傳動功率適當(dāng)降低。
安全系數(shù)定義為:
S
B=

…………………………(100)
式中:
ΘS——膠合溫度,單位為攝氏底(℃);
ΘBmax——最大接觸溫度,單位為攝氏底(℃);
Θoil——油溫,單位為攝氏底(℃)。
然而,齒輪的實際載荷與確定的接觸溫度之間的關(guān)系很復(fù)雜,用溫度的任何比值來表達安全系數(shù)可能會引起混淆。
因此,除了試驗載荷級的說明以外(見10.4節(jié)),建議用膠合溫度與計算的最大接觸溫度之間所要求的最小差別(如≥50K)來表達安全概念。
附錄A
(資料性附錄)
閃溫公式提示
自從最初的閃溫公式[12][14]公布以來,布洛克又作了下列修改:
——將赫茲接觸帶的全寬改為半寬,并用橢圓形磨擦熱分布的1.11代替拋特線形磨擦熱分布的0.83 =1.17[16];
——擴展到不同方向的切線速度[32]見式(3)。
為方便起見,作了確切的修改:
——有些量有另一些量來表達,如赫茲接觸帶半寬和曲率半徑;
——公式的某些部分被集中為獨立的系數(shù),如熱彈系數(shù),見A,3。