3.5 無量綱化
在工程分析計算中,位移、時間和力是基本量,其它是導(dǎo)出量,因此各無量綱化定義如下:
無量綱位移:Xj=xj/d0,Yj=yj/d0,Ljlj/d0,Dj=dj/d0;
無量綱時間:τ=Ωt;
無量綱剪力: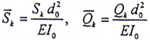
無量綱力矩: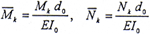
無量綱質(zhì)量和轉(zhuǎn)動慣量:
無量綱剛度系數(shù):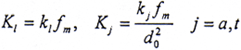
無量綱阻尼系數(shù):
無量綱轉(zhuǎn)動角速度:
=Ω/ωk;
其中:ωk為一階臨界轉(zhuǎn)速;
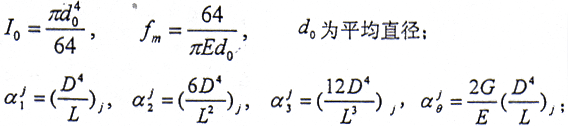
設(shè)系統(tǒng)方程的解為:x=x0eλt,λ=-u+iv;
則相應(yīng)的無量綱表達式為:
;
式中:
=λ/Ω=-U+iV,而 U=u/Ω,V=v/Ω。
經(jīng)上述過程后,將式(3.20)和式(3.21)無量綱化,就可以方便地寫出無量綱形式的系統(tǒng)運動微分方程。限于篇幅在此從略。
3.6 系統(tǒng)方程的求解
當(dāng){F}=0時,式(3.20)為自由振動方程,可以對系統(tǒng)進行模態(tài)分析。此時式(3.20)所對應(yīng)的特征值問題為
(λ2[M]+λ([G]+[C])+[K]+[S]){φ}=0 (3.29)
這是一個二次特征值問題,可以化為一般的廣義特征值問題求解。求解的方法有QR法、Lanczos法和廣義逆迭代法等,本文采用廣義逆迭代法[90]。
當(dāng){F}≠0時,可以對系統(tǒng)進行各種強迫振動分析。在轉(zhuǎn)子系統(tǒng)中,最主要的外激振力是轉(zhuǎn)子的不平衡而引起的慣性力,因此只要確定了轉(zhuǎn)子的不平衡量及其作用的位置,就可以計算系統(tǒng)的不平衡響應(yīng),常用的方法有振型疊加法、直接積分法和高斯消去法[90]。本文采用高斯消去法直接求解系統(tǒng)的不平衡響應(yīng)。
3.7 軸承—轉(zhuǎn)子—齒輪聯(lián)軸器系統(tǒng)的動力學(xué)分析
軸承—轉(zhuǎn)子—齒輪聯(lián)軸器系統(tǒng)的動力學(xué)分析包括系統(tǒng)的穩(wěn)定性和模態(tài)分析以及臨界轉(zhuǎn)速和不平衡響應(yīng)的計算等內(nèi)容。下面主要來討論齒輪聯(lián)軸器的動力特性對系統(tǒng)的影響。
計算模型如圖3.6所示。整體系統(tǒng)由一個齒輪聯(lián)軸器連接的二個Jeffcott轉(zhuǎn)子系統(tǒng)所組成,共有三跨,因此是一典型的多跨軸承—轉(zhuǎn)子系統(tǒng)。齒輪聯(lián)軸器的結(jié)構(gòu)近似選用CL5型,為方便問題的討論,重點分析左右對稱布置的系統(tǒng)。系統(tǒng)具體的結(jié)構(gòu)參數(shù)見表3.1。工作轉(zhuǎn)速為n=3000rpm。齒輪聯(lián)軸器對中良好,全齒寬接觸。計算采用無量綱化(在后面的計算中,如無特殊說明均為無量綱)。傳統(tǒng)上計算此類問題時往往采用兩種方法,第一種方法是將聯(lián)軸器人為截斷,只計算系統(tǒng)的左側(cè)或右側(cè)轉(zhuǎn)子[18,50],即單軸分析法,這樣系統(tǒng)為一單跨軸承—轉(zhuǎn)子系統(tǒng),系統(tǒng)靜定負(fù)荷分配簡單,但是卻忽略二轉(zhuǎn)子之間的耦合作用;第二種方法是整體分析法,這一方法是將整個系統(tǒng)作為研究對象,將齒輪聯(lián)軸器用一等效的軸段[6]來代替(故稱之為等軸法),等效軸段長度的剛度即為等效剛度,此時系統(tǒng)是超靜定的。從直觀上看這樣處理似乎比單軸分析法更為合理,但是其中等效軸段的長度不易確定。為便于比較在下文中凡涉及到等效軸法的計算結(jié)果均是以聯(lián)軸器的實際長度作為等效長度而得的。
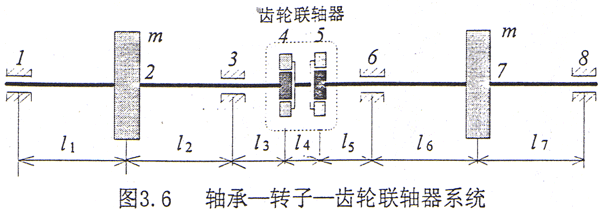
表3.1 對稱轉(zhuǎn)子系統(tǒng)的結(jié)構(gòu)參數(shù)
軸段及材料 |
圓盤 |
圓軸承 |
li=0.5m(i=1,2,6,7) |
軸徑 d=0.09m |
質(zhì)量 m=700kg |
長徑比 B/d=0.5 |
l3=l5=0.15m |
彈性模量E=206GPa |
極轉(zhuǎn)動慣量Jz=12.0kg·m2 |
間隙比 ψ=0.2% |
l4=0.15m |
泊松比 μ=0.3 |
赤道轉(zhuǎn)動慣量Jd=6.0kg·m2 |
動力粘度μ=0.0221Pa·s |
3.7.1 齒輪聯(lián)軸器對軸承特性的影響
對于對稱軸承—轉(zhuǎn)子—齒輪聯(lián)軸器系統(tǒng),計算步驟如下:1)軸心的平衡位置隨轉(zhuǎn)速的變化關(guān)系,結(jié)果如圖3.7所示。2)軸承的油膜剛度和阻尼系數(shù)隨轉(zhuǎn)速的變化關(guān)系,結(jié)果如圖3.8所示。由于在兩側(cè)轉(zhuǎn)子上對應(yīng)軸承的特性相同,故僅列出在左側(cè)轉(zhuǎn)子上二個軸承(#1和#2)處的結(jié)果。
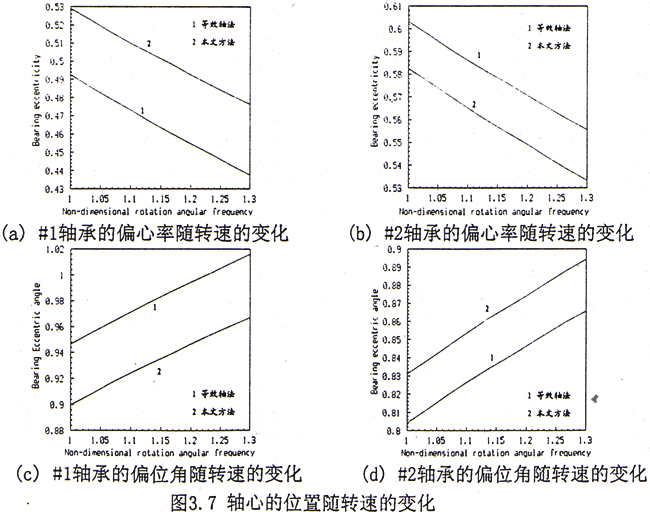
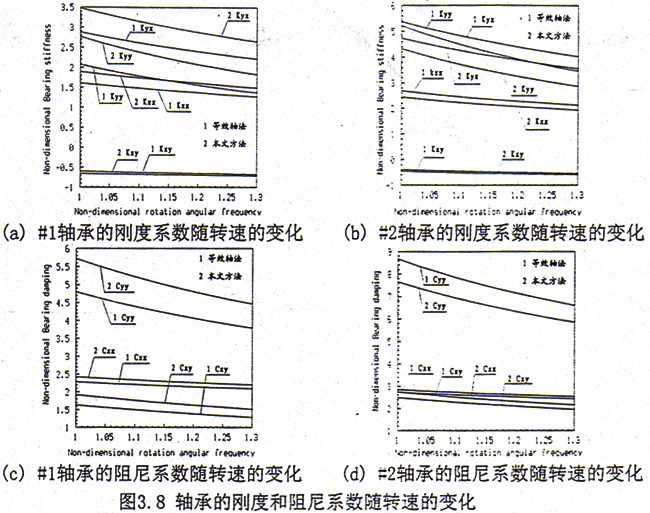
從以上的計算結(jié)果來看,用等效軸法計算軸承的軸心位置,#1軸承處的偏心率明顯偏小,偏位角偏大,而在#2軸承處則正相反。這表明采用等效軸法會使轉(zhuǎn)子的平衡位置產(chǎn)生較大的誤差,也預(yù)示著#1軸承和#2軸承之間負(fù)荷分配的變化。另外比較#1和#2軸承的結(jié)果,還可以看出,聯(lián)軸器的作用使得二個軸承的負(fù)荷分配趨于接近,而等效軸法從某種意義上講相當(dāng)于二個轉(zhuǎn)子的直接對接,必將造成二軸承負(fù)荷分配不均,在工作轉(zhuǎn)速下各軸承處的負(fù)荷分配見表3.2,因此對軸承的受力來說這也正是采用齒輪聯(lián)軸器的優(yōu)點所在。從二軸承處的動特性來看,#1軸承的各項剛度和阻尼系數(shù)比等效軸法大,而#2軸承的各項剛度和阻尼系數(shù)則比等效軸法小,這歸根到底也是軸承負(fù)荷分配發(fā)生了變化的結(jié)果。如果采用單軸分析方法計算,以左側(cè)轉(zhuǎn)子為例,由于聯(lián)軸器的質(zhì)量與圓盤相比要小許多,系統(tǒng)近似為一對稱轉(zhuǎn)子系統(tǒng),則作用在#1和#2軸承上的負(fù)荷相差不大,因此二個軸承處的動特性系數(shù)也比較接近。由于軸承的靜、動特性發(fā)生了變化,因此勢必引起系統(tǒng)動態(tài)特性的變化。
表3.2 工作轉(zhuǎn)速下各軸承處的負(fù)荷分配(kg)
|
#1軸承 |
#2軸承 |
#3軸承 |
#4軸承 |
本文方法 |
311.55 |
414.45 |
414.45 |
311.55 |
等效軸法 |
259.64 |
465.17 |
465.17 |
259.64 |
3.7.2 齒輪聯(lián)軸器對系統(tǒng)復(fù)特征值和復(fù)模態(tài)的影響
下面對二側(cè)對稱的軸承—轉(zhuǎn)子—齒輪聯(lián)軸器系統(tǒng)進行分析計算。
(1)按‘等效軸’法計算,結(jié)果見表3.3。
表3.3 按‘等效軸’法計算得不同轉(zhuǎn)速下系統(tǒng)的特征值
相對工作角速度Ω/ωk |
No. |
i=u/Ω+iv/Ω |
1.00000 |
1 2 3 4 |
-0.34774D-01+i0.72585D+00 -0.22925D-01+i0.76828D+00 -0.41981D-01+i0.83403D+00 -0.28089D-01+i0.85016D+00 |
1.43719 |
1 2 3 4 |
-0.83590D-05+i0.51463D+00 -0.15650D-02+i0.53676D+00 -0.27019D-01+i0.57455D+00 -0.23805D-01+i0.58722D+00 |
1.43819 |
1 2 3 4 |
0.35243D-04+i0.51430D+00 -0.15355D-02+i0.53639D+00 -0.26998D-01+i0.57414D+00 -0.23797D-01+i0.58681D+00 |
注:ωk=314.159 rad/s(不同)。
(2)不計齒輪聯(lián)軸器內(nèi)阻尼按本文方法計算,結(jié)果見表3.4。
表3.4 不同轉(zhuǎn)速下軸承—轉(zhuǎn)子—聯(lián)軸器系統(tǒng)的特征值
相對工作角速度Ω/ωk |
No. |
i=u/Ω+iv/Ω |
1.00000 |
1 2 3 4 |
-0.19310D-01+i0.63059D+00 -0.14980D-01+i0.64585D+00 -0.18366D-01+i0.72318D+00 -0.65746D-01+i0.80639D+00 |
1.26417 |
1 2 3 4 |
-0.14454D-04+i0.50838D+00 -0.44376D-03+i0.51607D+00 -0.16639D-01+i0.57032D+00 -0.57178D-01+i0.62901D+00 |
1.26517 |
1 2 3 4 |
0.35627D-04+i0.50801D+00 -0.40779D-03+i0.51568D+00 -0.16633D-01+i0.56986D+00 -0.57150D-01+i0.62848D+00 |
比較上述二種情況,可以看出在工作轉(zhuǎn)速Ω/ωk=1.0時,表3.3所列系統(tǒng)低階特征值的實部和虛部的絕對值明顯要大于表3.4所對應(yīng)的值,這表明:1)在正常工作狀態(tài)下,按等效軸法計算得的系統(tǒng)對數(shù)衰減率和固有頻率要大。按等效軸法計算,在Ω/ωk=1.43819時系統(tǒng)失穩(wěn);而按本文的模型,即使在全齒寬接觸的情況下,系統(tǒng)的失穩(wěn)轉(zhuǎn)速也只為Ω/ωk=1.26517,這說明用等效軸法來計算這類系統(tǒng)的失穩(wěn)轉(zhuǎn)速,數(shù)值明顯偏高,是極不合適的。2)通過比較Ω/ωk=1.0時,低階固有頻率值的數(shù)值可以推出,按等效軸法所計算得的系統(tǒng)的低階臨界轉(zhuǎn)速也是偏高的,這一現(xiàn)象在一實際的軸承—轉(zhuǎn)子—齒輪聯(lián)軸器系統(tǒng)中被證實[66],因為等效軸法實質(zhì)上相當(dāng)于齒輪聯(lián)軸器被鎖定時將二個轉(zhuǎn)子看成為一個整體,這樣處理相當(dāng)于給系統(tǒng)增加了一個約束,結(jié)果自然會失真。關(guān)于系統(tǒng)的臨界轉(zhuǎn)速在后面我們還將作詳細(xì)的討論。如果按單軸分析法計算,系統(tǒng)的失穩(wěn)轉(zhuǎn)速Ω/ωk=1.19215。因此用等效軸法(按聯(lián)軸器的實際長度作為等效長度)和單軸分析法所計算得的系統(tǒng)失穩(wěn)轉(zhuǎn)速實質(zhì)上是二個極限,前者偏高不安全,而后者偏低過于保守。
(3)齒輪聯(lián)軸器的內(nèi)阻尼對系統(tǒng)失穩(wěn)轉(zhuǎn)速的影響
齒輪聯(lián)軸器的內(nèi)阻尼系數(shù)可由上一章的方法計算。總的來說,聯(lián)軸器的內(nèi)阻尼受系統(tǒng)工況的影響較大,在不同的工況下內(nèi)阻尼會有所變化。設(shè)各齒承載相同,即聯(lián)軸器對中良好,其中扭矩T取為CL5型齒輪聯(lián)軸器許用扭矩的一半;按照文獻[34],齒面間的滑動摩擦系數(shù)取為f=0.15;ω應(yīng)為轉(zhuǎn)動角速度與最易產(chǎn)生失穩(wěn)的渦動角速度之差,失穩(wěn)一般首先發(fā)生在低階,在此渦動頻率取為第一階固有頻率。相對橫向振幅為CL5型聯(lián)軸器[88]內(nèi)外齒輪之間的徑向間隙c,相對轉(zhuǎn)角振幅為arctg2c/l,其中l(wèi)為內(nèi)外齒輪的接觸寬度。這樣可以計算得到在工作轉(zhuǎn)速下無量綱內(nèi)阻尼系數(shù)為Cl=0.38,Ca=3.67×10-3。系統(tǒng)的失穩(wěn)轉(zhuǎn)速見表3.5。
表3.5 不同轉(zhuǎn)速下軸承—轉(zhuǎn)子—聯(lián)軸器系統(tǒng)的特征值
相對工作角速度Ω/ωk |
No. |
i=u/Ω+iv/Ω |
1.00000 |
1 2 3 4 |
0.19315D-01+i0.63062D+00 -0.14968D-01+i0.64611D+00 -0.19918D-01+i0.72273D+00 -0.66795D-01+i0.80548D+00 |
1.26317 |
1 2 3 4 |
0.21974D-04+i0.50879D+00 -0.14346D-03+i0.51674D+00 -0.18046D-01+i0.57034D+00 -0.57988D-01+i0.62870D+00 |
1.26417 |
1 2 3 4 |
0.30147D-04+i0.50842D+00 -0.10558D-03+i0.51636D+00 -0.18039D-01+i0.56988D+00 -0.57959D-01+i0.62818D+00 |
比較表3.4和表3.5二種情況,系統(tǒng)的失穩(wěn)轉(zhuǎn)由1.26517降為1.26417,顯然變化很小。而且失穩(wěn)時的渦動頻率也幾乎不變。如果將各內(nèi)阻尼系數(shù)增大為原來的5倍,則失穩(wěn)轉(zhuǎn)速在ω/ωk=1.23417~1.23517之間。由此可見,在對中良好并且內(nèi)外齒輪間潤滑充分時,聯(lián)軸器內(nèi)阻尼對系統(tǒng)失穩(wěn)轉(zhuǎn)速的影響不十分明顯。當(dāng)然在潤滑失效并且對中不良時,由于偏載效應(yīng)而引起齒面間的摩擦力(力矩)可能要大得多[6],此時內(nèi)阻尼系數(shù)也會相應(yīng)增大。
(4)齒輪聯(lián)軸器耦合系統(tǒng)的復(fù)模態(tài)
在ka=0.128不計內(nèi)阻尼時,工作轉(zhuǎn)速下系統(tǒng)的前12階彎曲振動復(fù)模態(tài)圖見圖3.9。從復(fù)模態(tài)圖上可以看出,在低階彎曲模態(tài)中,輪齒的變形是較小的,輪齒變形較大主要發(fā)生在高階模態(tài)中。這與實際情況比較接近,因為在實際的轉(zhuǎn)子系統(tǒng)中,輪齒的剛度一般比軸段的剛度要大許多,因此在低階的彎曲模態(tài)中,輪齒的變形體現(xiàn)不出來。系統(tǒng)前2階的扭轉(zhuǎn)振型如圖3.10所示。在前二階扭轉(zhuǎn)振型中輪齒變形也較小。
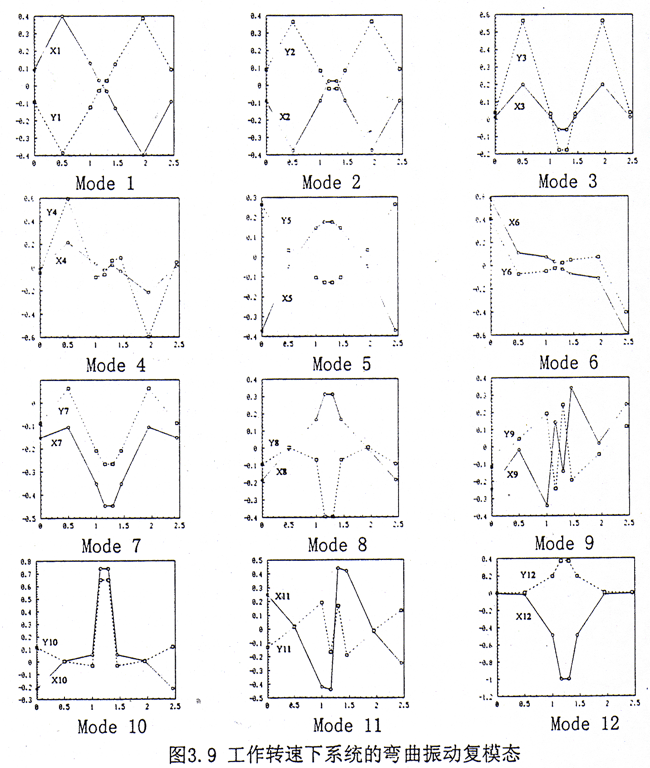
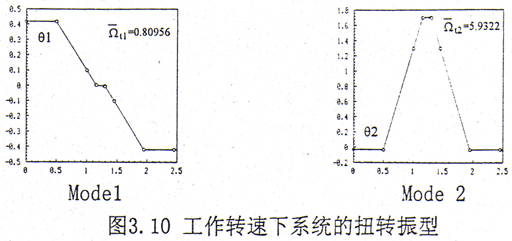
上一頁
下一頁